Devon Tandberg
General Aviation Modular Electric Tow Bar
2019-2020 CWU Senior Project
Project Analysis
There are many important areas of this project that need analyzing. These included finding the total forces required to move a fully loaded 1958 Cessna 175, and the torque needed to supply the wheels of the device with enough power to allow for that movement. Once these values were found, the rest of the device could be analyzed and designed.
When analyzing and designing the rest of the project, many things needed to be considered. Stress is the first main consideration, and finding a minimum cross sectional area for each piece of framing material. This same idea can be applied to the analysis of the shaft that is connected to a worm gear system. The worm gears need to be able to handle the forces exerted on them from a drill powering the system, and the shaft needs to be of a diameter able to handle the forces exerted from the torque being applied to it, and the forces exerted from the from the bearings supporting the shaft, and the forces the worm gear has on the system as well.
Along with the designing of the worm gears based on forces, the worm gear must be able to work at a certain speed. In the case of this project, a 20:1 gear reduction from the drill powering the system is needed to allow the plane to move at a desired speed of 0.5 m/s.
There are many other areas of analysis that are needed in project, and the areas stated above are just a summary. If you would like more information about the analysis of this project, please see the link to the full report on this project on the Home page, and refer to Appendix A. All of the analysis's of this project are located there in full detail. You can also see an example of an analysis below.
Analysis Example (RADD)
This project used a RADD system to ensure engineering merit was used in the project. An example can be found below.
Analysis A-1: Total Force Required to Maneuver Plane
Requirement: A total force is required to accelerate a 1827 lb 1958 Cessna 175 from rest to a speed of approx 1 mph (0.5 m/s), with an acceleration of 0.1 m/s^2. It is this value that will be the basis of the rest of the projects analysis and design.
Analysis: Analysis A-1 reveals that a total force of 73.4 lb (326.48 N) is required to accelerate a plane from rest to 0.5 m/s in 5 total seconds. This force can also be applied in the opposite direction and allow for the plane to be pushed as well as pulled by the user of the device.
Design: This analysis is the basis to all the part designs in this project. The tow bar must have a cross sectional area that is big enough to support the stresses involved in a tensile and compression state, and not buckle or yield because of it, and the frame of this device must be able to support any forces and stresses as well.
Documentation: You can find Analysis A-1 in the figure to the right, and as well in Appendix A of the report (link to it is on the Home page), along with all part drawings and assembly drawings.

More Analysis's

RPM Required for Linear Motion Analysis
Torque Required for Wheels to Spin Analysis

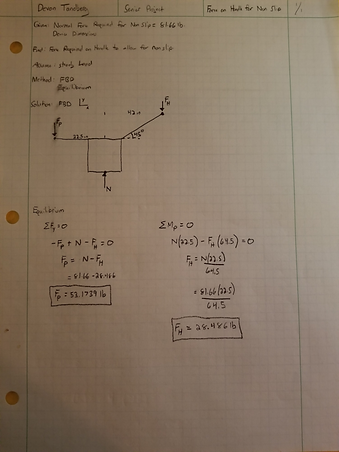
Normal Force Required on Handle Analysis
Torque on Shaft Analysis


Worm Gear Stress Analysis
Frame and Worm Gear Idea Drawing


Tow Bar Attachment Idea Drawing
Design Process
One of the main portions of this design was what the framing material will be made out of. At first, it was designed using aluminum rectangular tubing, and machining each piece to size and specifications. This would allow for fasteners to be inserted and used, and allow everything else to be attached to these pieces. This design was almost taken to completion, however before that happened, it was believed that this would take up far too much time to have to make each individual piece of the frame. The overall design/shape did not change, and you can see on the home page that having to make individual piece would have been time consuming. Because of this, a new direction for materials and manufacturing needed to be developed, and that is when T Slot framing was found. This new material made it easy in manufacturing as it is already designed to be fastened together with pre-made brackets and fasteners, and only needed to be cut to specified lengths. This also made it so the design could have smaller tolerances, as each bracket would now be bought and not hand made. This would allow for the overall design to be a little smaller. This change overall made this project much more expensive, as having to buy individual brackets brought a hefty cost, however, it saved many, many hours on the manufacturing side, making this project both look and work better, but also easier to work with.